Los tratamientos térmicos son los más empleados en la metalurgia a día de hoy para modificar la microestructura y constitución de metales y aleaciones sin modificar su composición química. Usan solamente la temperatura como variable. Así al calentar el material se logran las modificaciones requeridas. El recocido, el temple, el revenido y el normalizado son los tratamientos térmicos más comunes.
¿Qué es el recocido de metal?
El recocido es un tratamiento térmico mediante el que se calienta el metal hasta una temperatura determinada durante un período también definido, para después enfriarlo poco a poco. Se emplea para modificar las propiedades mecánicas, eléctricas y magnéticas del metal, pero los objetivos del recocido del metal pueden ser varios: desde rebajar la dureza a eliminar tensiones residuales protudidas en otros tratamientos, aumentar la tenacidad, la ductilidad o la plasticidad, obtener un grano más fino o reducir la segregación. Asimismo, con el recocido de los aceros se busca además ablandar las piezas para conseguir un maquinado más fácil y obtener determinadas propiedades mecánicas.
Fases del proceso de recocido del metal
Son fundamenalmente tres:
- Calentamiento hasta una temperatura determinada.
- Mantenimiento de la temperatura durante el tiempo necesario.
- Enfriamiento progresivo, realizado con la velocidad adecuada, hasta llegar a la temperatura ambiente.
El tiempo es la variable clave, tanto en el calentamiento y en el enfriamiento. A lo largo del proceso, la temperatura varía en el material, por lo que el tiempo y la rapidez con la que se calienta o enfría dependerá del tamaño y forma de la pieza. Esto es algo muy a tener en cuenta puesto que si la temperatura cambia muy rápidamente pueden generarse tensiones internas, que redundan en deformaciones y hasta grietas. En resumen, la duración del proceso de recocido debe ser suficientemente larga para conseguir la modificación adecuada del material.
Tipos de recocido de metal
El recocido también se emplea para reducir defectos que se hayan producido durante el conformado en frío, restando dureza y aportando ductilidad a los metales más agrietados. En estos casos se producen recristalizaciones y se emplean temperaturas relativamente bajas, para que no se produzcan deformaciones en el enfriamiento. Estos son los tipos de recocido de metal habituales:
Recocido de eliminación de tensiones
Consiste en calentar el metal entre 550º y 650ºC durante entre 30 y 120 minutos, para después enfriarlo progresivamente, con el objetivo de eliminar tensiones internas del material.
Recocido de ablandamiento
Tanto los aceros con alto contenido de carbono como la mayoría de aceros de alta aleación son difíciles de mecanizar. Con un proceso de recocido de ablandamiento se reduce su dureza, para facilitar así el mecanizado. Se puede aplicar en acero y también en aleaciones de cobre y latón. Así, se calienta el material entre 650 y 750ºC durante 3-4 horas.
Recocido normal
Con este proceso se mitigan las consecuencias de las deformaciones tras operaciones de transformación en caliente como la fundición o la forja, sobre todo en el caso de aceros al carbono. También sirve para afinar el grano. El recocido normal consiste en un calentamiento a temperaturas de entre 750º y 980ºC según el contenido de carbono del material. A continuación, se mantiene la temperatura, para pasar a un enfriamiento lento a temperatura ambiente.
Recocido por cortocircuito
Se usa para ablandar aquel cobre que va a tener usos eléctricos, mejorando su conductividad. Se trata de recocer el material a una temperatura levemente superior a los 400 ºC, tras lo que se procederá a un enfriamiento rápido. El recocido por cortocircuito aporta numerosas ventajas, como una mayor velocidad de producción y la reducción de los tiempos muertos.
En los Centros de servicios de Alsimet en Parla (Madrid) y Molins de Rei (Barcelona) ofrecemos distintos acabados y tratamientos para cubrir las necesidades de todo tipo de sectores industriales.
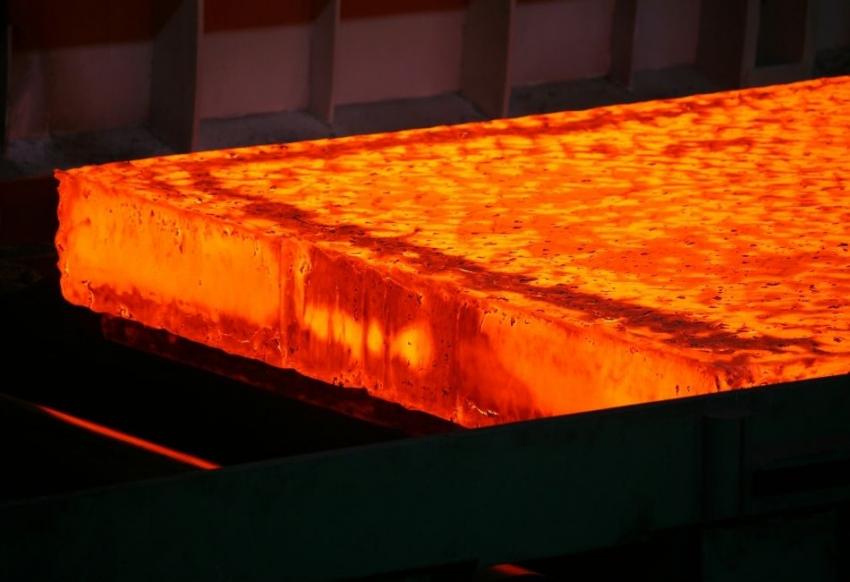