El sector minero y el metalúrgico son dos de los mayores consumidores de energía y emisores de gases de efecto invernadero. Crear y adoptar tecnología que reduzca ese impacto ambiental y social (la minería puede suponer riesgos para poblaciones y regiones) es inexcusable. Además, ambas actividades consumen grandes cantidades de agua, otro desafío más para las empresas del sector, que tienen que cumplir cada vez requisitos de sostenibilidad más exigentes y ser más eficientes.
Una apuesta por las energías renovables y la eficiencia energética
En cualquier explotación minera o instalación industrial metalúrgica el consumo de energía supone buena parte de los costes de producción, por los que instaurar estrategias de ahorro puede suponer una mejora sustancial. Históricamente, España ha sido un país muy dependiente de energías fósiles, que ha tenido que importar masivamente. La incorporación de energías renovables, de hidrógeno verde así como de planteamientos de economía circular no solo es viable desde el punto de vista económico. También es un aliciente para atraer nuevo talento y propuestas innovadoras al sector. Así, la digitalización de las operaciones, el análisis con big data yhasta la aplicación de la inteligencia artificial se convierten en una fuente de oportunidades para la industria metalúrgica.
Uno de los sectores con un consumo más alto de energía y de generación de CO2, el acero, integra ya los objetivos de eficiencia energética en sus estrategias comerciales. No en vano, según datos de Worldsteel, la energía representa el 15-20% del costo total de producción de acero.
Sin ir más lejos, ArcelorMittal se marcó un objetivo de reducción de emisiones en Europa en un 30%, con la meta del 2050 para alcanzar la neutralidad de carbono. El acero es 100% reciclable y de forma infinita, y resulta imprescindible para la fabricación de turbinas eólicas o paneles solares que son clave para un futuro más sostenible. Aún así, Wordsteel estima que la industrial del acero genera entre el 7 y el 9% del total de las emisiones globales de carbono. Eso sí, se está en el camino: según UNESID, las emisiones de CO2 por tonelada de acero producido han descendido un 75% en los últimos 50 años.
Además, se calcula que la fundición de metales utiliza cerca del 4% de la energía mundial y produce sobre el 7% de las emisiones globales de GEI. Por esta razón es vital que la electricidad provenga de energías renovables, puesto que con ese proceso no se emite dióxido de carbono. Asimismo, la fundición de metales también puede realizarse por inducción y, es posible unificar en un proceso la tarea de fundir y la de derretir (en vez de fundir el mineral para hacer metal, derretir el metal para elaborar el material y después derretir ese material para elaborar los productos). Así se obtendrían no solo beneficios ambientales, también económicos.
Procesos innovadores, sostenibles y eficientes para descarbonizar el sector
El proceso para la fundición de aluminio es el mismo desde el siglo XIX. El material se obtiene con una disolución de óxido de aluminio y mineral de aluminio en criolita fundida, a través de electrodos de carbono. Así, la industria del aluminio produce hasta un 1% de las emisiones globales. Aunque en gran medida el impacto de carbono se debe al consumo energético, hasta un 20% de sus emisiones se producen durante el proceso de fundición y la degradación de los ánodos de carbono.
El ARPA-E ya lleva tiempo trabajando en procesos de fundición de metales que solo usan aire, agua y energía limpia, así como en procesos basados en electrólisis para evitar la emisión de gas de efecto invernadero. La transformación de procesos que llevan un siglo basándose en el uso de carbono, como el aluminio, el acero o muchas aleaciones es sin duda todo un reto.
La Ley de Cambio Climático y Transición Energética es el marco legal para la descarbonización de la economía española y su transición a un modelo circular. Con el apoyo del Plan Nacional de Energía y Clima, esta Ley impulsará las energías renovables, clave para descarbonizar el sector siderúrgico, además de la reducción de las emisiones y el desarrollo hidrógeno verde que sustituya a los combustibles fósiles. Sin embargo, el coste de la energía eléctrica en España sigue siendo una barrera que se intenta salvar con la creación del Estatuto de Consumidores Electrointensivos. Su objetivo, contar con un marco normativo que dé opción a nuevos esquemas de ayuda compatibles con las directrices europeas, para posibilitar una competencia justa con el resto de Europa (que no tiene que asumir los costes del CO2), conseguir más estabilidad operacional y fomentar las inversiones necesarias para cumplir con los hitos de la descarbonización.
Entonces, ¿cómo cumplir de forma eficaz con el acuerdo de París?
No hay una única solución con la que reducir de forma drástica las emisiones de CO2 del sector, pero hay una serie de elementos que, combinados, pueden generar una transformación industrial con repercusiones en el medio ambiente y en la calidad de vida de las personas. Reducir el impacto de la industria pasa por rebajar al mínimo la reducción de emisiones. Para ello es necesario mejorar la eficiencia de los procesos, aumentar el uso de la chatarra e invertir en tecnología e innovación.
Además, la eficiencia y la circularidad pasan por más reutilización, remanufactura y reciclaje. Apostar por el ecodiseño, teniendo en cuenta todo el ciclo de vida del producto, incluido el fin de su vida útil, también es fundamental para lograr una mayor eficiencia de los materiales.
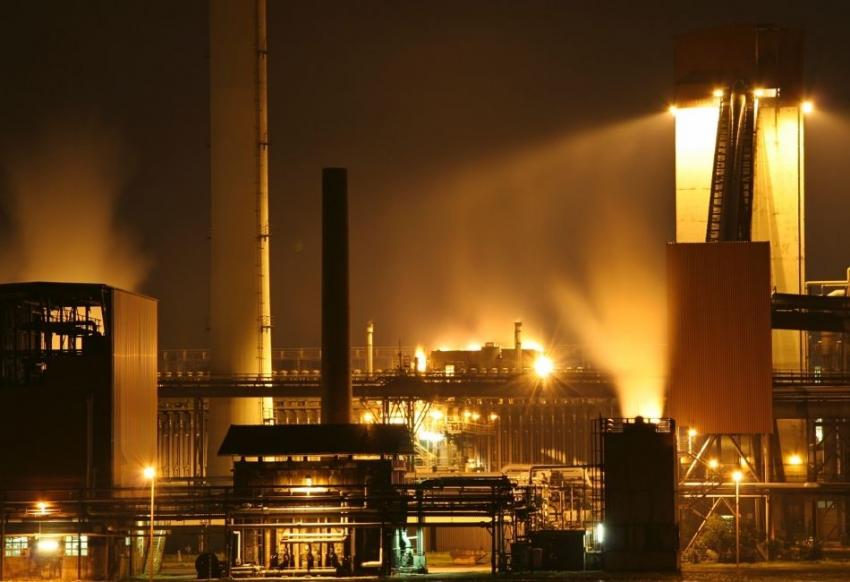