El aluminio ha tenido un papel clave en el desarrollo de la aviación. Ya estuvo presente en el primer vuelo de la historia en 1903, en el avión de los hermanos Wright. El ingenio tenía un motor automático de cuatro cilindros y 12 caballos de fuerza modificado con un bloque de aluminio para reducir el peso. Con los rápidos avances desde principios del siglo XX, el aluminio empezó a reemplazar muy pronto al acero y a la madera. Tanto es así que, en 1920, se construyó el primer avión completamente de este material. Sin duda, la ligereza, la resistencia y la manejabilidad de este metal lo convierten en ideal para la aviación.
Pero hay más: las aleaciones de aluminio pueden alcanzar una extraordinaria resistencia, soportando las presiones y tensiones que implican los vuelos. Además, múltiples elementos del interior de la aeronave se fabrican con este material para ahorrar peso y, por tanto, combustible y emisiones. Así, el aluminio se ha convertido en el material más empleado en los aviones, por lo que puede llegar a sumar hasta el 80 % del peso de un avión sin carga.
Otra ventaja es que el aluminio resiste la corrosión, por lo que algunas aerolíneas no pintan sus aviones y así consiguen ahorrar unos cuantos kilos de peso.
La demanda de aluminio para el sector aeronáutico, en constante crecimiento
Se prevé que en las próximas dos décadas se duplique la flota mundial de aviones y el número anual de pasajeros. Países como India, China y aquellos de Oriente Medio, Asia y Pacífico que están experimentando una mejora en su calidad de vida, son ya una fuente de demanda creciente. Al mismo tiempo, la necesidad de reducir las emisiones a la atmósfera y el ruido, además de ajustar los costes de mantenimiento, exige la optimización de las soluciones de diseño para las próximas generaciones de aeronaves. A esto hay que sumar que, a más viajes aéreos, más aeronaves, pero también más inversión en infraestructuras (aeropuertos, control aéreo, etc.). Sin duda todo esto provocará también un aumento en la demanda del aluminio para construcción.
En esta línea se han desarrollado súper aleaciones de aluminio, pero también materiales innovadores. Estos últimos son sensiblemente más caros de producir, como por ejemplo los compuestos termoestables, que pueden llegar a costar 15 veces más que el aluminio mecanizado, y hasta 75 veces en el caso de los termoplásticos. En este sentido, la mayor ligereza de este tipo de materiales con respecto al aluminio, su mayor resistencia a la corrosión y su alta resistencia, han hecho que cobraran mucho protagonismo en la última generación de aeronaves (Boeing 787 y Airbus A 350). Su alta flexibilidad los convierte en una gran opción a la hora de crear estructuras eficientes, si bien presentan problemas de delaminación, daño por impacto, así como dificultad para la reparación y el reciclaje. Todo esto hace que al menos de momento el aluminio siga siendo una opción muy eficaz y fiable, además de la más rentable por su relación peso/ coste frente a materiales no metálicos como la fibra de carbono.
Por tanto, aunque la sustitución del aluminio por nuevos materiales vaya en aumento, al seguir creciendo la demanda de producción de aviones, se seguirá manteniendo una demanda fuerte de este metal. También la animará su reciclabilidad, clave para conseguir un sector cada vez más sostenibles.
¿Qué aleaciones de aluminio se usan en los aviones?
Las aleaciones de alta resistencia, sobre todo el aluminio 7075 o zicral, que consigue un extra de resistencia gracias a la adición de zinc y cobre, permiten reforzar las estructuras de las aeronaves, desde las alas al fuselaje o los motores deflectores, pero hay más. Se identifican con un sistema de numeración de cuatro dígitos, que indica qué tratamiento térmico han recibido, cuál es su composición y cuáles son sus propiedades mecánicas. Estas son las aleaciones de aluminio más usadas en los aviones y sus propiedades:
- 2024-T3. Es la más común de las aleaciones de aluminio de alta resistencia, con un alto grado de calidad y muy indicada para aviones por su resistencia y resistencia a la fatiga. Eso sí, su resistencia a la corrosión es inferior al del aluminio 6061. Se usa para revestimientos de fuselaje y alas, capós, estructuras de aeronaves y también para reparación y restauración, por su acabado brillante.
- 6061-T6. Con una muy buena buena resistencia a la corrosión, permite soldadura, no como en el caso anterior. Su resistencia es similar a la del acero dulce. Las aplicaciones más típicas son en colchonetas de aterrizaje, carrocerías y marcos de camiones, además de elementos estructurales.
- 5052-H32. No es estructural, y tiene una mayor resistencia a la fatiga que la mayoría de las aleaciones. También es muy resistente a la corrosión, sobre todo en entornos marinos. La chapa de aluminio 5052-H32 se emplea mucho en la construcción de tanques de combustible.
- 3003-H14. Es aluminio puro con manganeso añadido, para lograr mayor resistencia. Es la más usada de las aleaciones de aluminio, resulta muy fácil de trabajar, de embutir, hilar y soldar. Se utiliza para cubiertas y placas deflectoras.
- 7075. Muy usada para reforzar estructuras de aluminio de las aeronaves, contiene cobre (1,6 %), magnesio (2,5 %) y zinc (5,6 %) para lograr la máxima resistencia. Tiene una excelente maquinabilidad y un acabado muy agradable.
Sin duda, en los próximos años veremos aviones sin un material predominante, no como sucedía hasta ahora con las aleaciones de aluminio. Los materiales compuestos han llegado para quedarse, pero sigue siendo un desafío el uso de los composites junto al aluminio, sobre todo en lo que se refiere a la unión de ambos materiales.
En Alsimet ofrecemos productos de aluminio para usos industriales en forma de barra, chapa, cinta y pletina. Consulte con nuestras delegaciones para realizar pedidos a su medida.
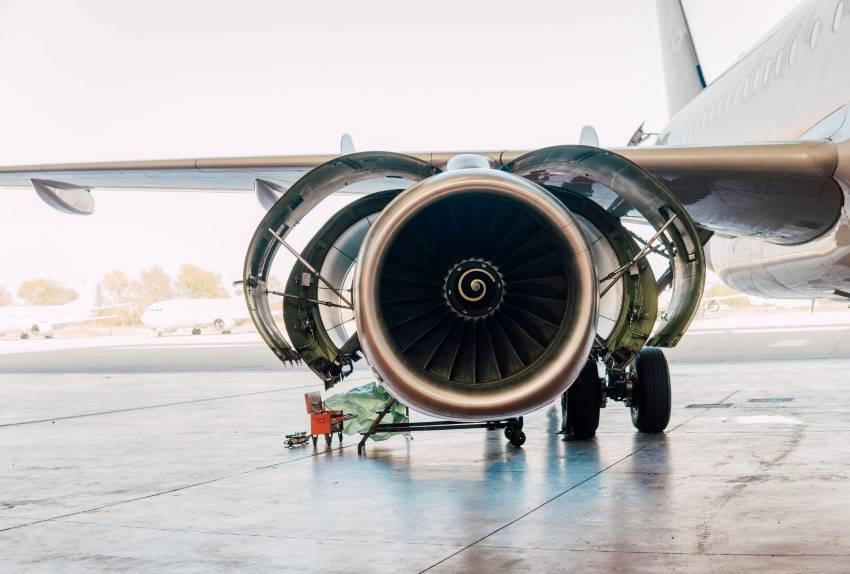